
TST Seal :
- Fireproof
- Cable fixinAg
- Watertight
- Airtight
- Dustproof
- Noise reduction
- Vibration reduction
- Pressure resistance
- Corrosion resistance
- EMI/EMP
- Pest & rodent resistance
Related Articles
- circular seal (7)
- flange sealing (1)
- industrial sealing (2)
- rectangular seal (20)
- sealing modules (21)
- sealing solution (5)
Cable sealing module for strong corrosive environment TST Seal anti-corrosion sealing system application
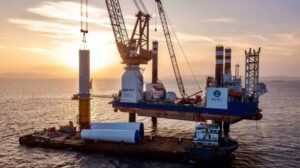
In the petrochemical industry, corrosion is like an “invisible killer”, threatening production safety and equipment life at all times. From the distillation tower of the refinery to the deep-sea oil and gas pipeline, from the acidic medium storage tank to the high-temperature reactor, the corrosive environment is everywhere. With its innovative materials and precise design, the TST seal modular cable and pipe penetration sealing system has created a double barrier of corrosion resistance, fire prevention and explosion prevention for petrochemical equipment, becoming a “weapon” for the industry to cope with complex working conditions.
01. Petrochemical corrosion area
The corrosion problems in the petrochemical industry are caused by the combined effects of medium characteristics, environmental conditions and process parameters, and can be mainly divided into the following types:
Corrosion of low-temperature light oil parts
Corrosion mechanism: In the light oil area of ≤120℃, HCl, H₂S and water form an acidic environment, resulting in uniform thinning or local perforation of the equipment.
Typical scenarios: atmospheric tower top condensation system, vacuum tower volatilization line, catalytic cracking fractionation tower top, etc.
High-temperature sulfur corrosion
Corrosion mechanism: In heavy oil parts above 240℃, sulfur, hydrogen sulfide and mercaptan react chemically with metals to form a sulfide corrosion layer.
Typical scenarios: heating furnace tubes, distillation tower feed section, hydrogenation reactor, etc.
Sulfur-containing flue gas corrosion
Corrosion mechanism: SO₃ and CO₂ generated by fuel combustion combine with water vapor to form sulfuric acid dew point corrosion on the surface of the equipment.
Typical scenarios: heating furnace air preheater, flue gas duct elbow.
Soil and stray current corrosion
Corrosion mechanism: buried pipelines are affected by soil electrolytes, microorganisms and stray currents, resulting in electrochemical corrosion.
Typical scenarios: long-distance pipelines, tank foundations.
Special medium corrosion
Corrosion mechanism: wet hydrogen sulfide environments containing HCN and Cl⁻ induce stress corrosion cracking (SSC), or high-temperature hydrogen environments cause hydrogen embrittlement.
Typical scenarios: absorption stabilization system, high-pressure pipelines of hydrogenation units.
02. Transit seal: the “first line of defense” against corrosion
Cable and pipe penetration is an inevitable part of the device, but traditional sealing methods (such as stuffing boxes, fireproof mud) have fatal defects in strong corrosive environments:
Material failure: ordinary rubber or fireproof mud, fireproof bag, etc. are easily corroded by acid, alkali, and oil media, resulting in reduced sealing performance;
Structural hazards: fixed seals cannot adapt to the thermal expansion and contraction or vibration of the pipeline, causing gap leakage;
Maintenance difficulties: on-site fire modification costs are high and the cycle is long, which is difficult to meet the rapid response needs of high-risk areas.
Therefore, the penetration sealing system must have the characteristics of corrosion resistance, high temperature resistance, and deformation resistance at the same time to effectively block the penetration of corrosive media and prevent fire and explosion accidents.
03. TST seal modular sealing system ensures petrochemical safety.
Targeting the pain points of the petrochemical industry, TST seal has launched a modular cable and pipe penetration sealing system, breaking through traditional limitations with dual innovations of “materials + structure”:
1. High-performance materials to resist corrosion in all scenarios
EPDM: low-smoke, halogen-free formula, resistant to acid, alkali, salt and oil media, and long-term tolerance to -40℃~120℃ temperature fluctuations;
Metal parts anti-corrosion: 316L stainless steel frame with passivated surface, suitable for salt spray and humid environments.
2. Modular design, adaptable to complex working conditions
Dynamic variable diameter technology: A single module can cover φ10~φ150mm cables/pipes, support later expansion and adjustment, and avoid secondary opening;
Redundant installation structure: reserve expansion compensation space to absorb pipeline thermal displacement and reduce stress concentration;
Multiple combination solutions: support free matching of functional modules such as fire protection, corrosion protection, and electromagnetic shielding to meet differentiated needs.
3. High-level certification, no worries in harsh environments
Passed international certifications such as China Classification Society (CCS) and Russian Maritime Register (RS), suitable for harsh scenarios such as offshore platforms and tankers;
Fireproof performance reaches A-60 (2/3 hours fire resistance), protection level IP68, and can withstand 0.5MPa pressure.
4. Simplify installation and reduce full-cycle costs
Standardized components: factory prefabricated modules, plug-and-play on site, and installation efficiency increased by 60%;
Maintenance-free design: material life is up to 30 years, reducing the frequency of shutdown and maintenance;
Flexible expansion: modules can be replaced by single-side operation, suitable for renovation and expansion projects.
5. Full life cycle service
Provide one-stop service for corrosion risk assessment, sealing solution design, installation and commissioning, and after-sales maintenance;
The core team has military-grade sealing experience and customizes solutions for special working conditions (such as high-pressure hydrogenation and deep-sea risers).
In the field of petrochemicals, corrosion prevention and control are closely related to safe production. TST seal modular cable and pipe penetration sealing system adopts the concept of “prevention first” to provide reliable sealing protection for high corrosion areas. Whether it is the complex working conditions of land refineries or the harsh environment of deep-sea platforms, TST seal has always helped the industry reduce costs and increase efficiency with technological innovation, protecting every inch of “lifeline”.
If you want to learn more about TST seal cable and pipe penetration sealing system, please send an email to contact us and receive industry application solutions and information for free. We will serve you wholeheartedly!